Crushers
JAW B-SERIES
JAW B-SERIES
Applications
- Granite, Basalt and most medium and hard stone
- Quarrying and mining
- Concrete and landfill recycling
- Construction waste
- Demolition
- Primary crushing
- Gravel
- Coal, slag and others

– Global leader in the 30 tonnes class
– Feed size up to 500 mm (20”)
– Feed opening 1.000 x 600 mm (40” x 24”)
– C.S.S min. – max. 45 – 170 mm (1 3/4” – 7″)
– Capacity up to 300 tonnes / hour
– Optional Hybrid drive, electric driven conveyors and magnet and plug out available for electric driven stacker or screen
– Optional Independent double deck vibrating pre-screen
– Compact and easy to transport without permit
– Lowest fuel consumption in the industry
– Best product shape possible
– Intake hopper suitable for wheel loader and excavator, 4 m³
– Hydraulic gap adjustment to safely prevent clogging
– High reliable closed circuit smooth drive of jaw crusher
– Smart sequential auto start/stop from remote
– Ability to track while producing
– 2 speed track drive
– Extensive option list to configure to your application
– Feed size up to 600 mm (24”)
– Independent double deck vibrating pre-screen 2.300 x 1.000 mm (8’ x 3’)
– Feed opening 1.100 x 700 mm (44” x 28”)
– C.S.S min. – max. 45 – 160 mm (1 3/4” – 6″)
– Capacity up to 400 tonnes / hour
– Full hybrid electric driven, energy saving version available
– Hydraulic sliding frame for service access under the feeding and scalping unit
– Intake hopper suitable for wheel loader and excavator, 5 m³
– Hydraulic gap adjustment to safely prevent clogging
– Smart sequential auto start/stop from remote
– Ability to track while producing
– 2 speed track drive
– Extensive option list to configure to your application
– Removable engine /generator compartment on full hybrid e version
– Feed size up to 700 mm (28”)
– Independent double deck vibrating pre-screen 2.300 x 1.000 mm (8’ x 3’)
– Feed opening 1.100 x 800 mm (44” x 32”)
– C.S.S min. – max. 70 – 175 mm (3”-7”)
– Capacity up to 420 tonnes / hour
– Full hybrid electric driven, energy saving version available
– Heavy duty quarry machine
– Intake hopper 5 m³
– Smart sequential auto start/stop from remote
– Ability to track while producing
– Hydraulic gap adjustment to safely prevent clogging
– 2 speed track drive
– Extensive option list to configure to your application
– Feed size up to 800 mm (32”)
– Vibrating feeder (4.390 mm) with 2 step grizzly 2.200 x 1.080 mm (7’ x 4’)
– Feed opening 1.100 x 900 mm (44” x 35”)
– C.S.S. min. – max. 120 – 210 mm (5”-8”)
– Capacity up to 450 tonnes / hour
– Feeding unit can be transported seperately
– Intake hopper 6 m³
– Smart sequential auto start/stop from remote
– Ability to track while producing
– Hydraulic gap adjustment to safely prevent clogging
– 2 speed track drive
– Extensive option list to configure to your application
– Vibrating feeder with 2step grizzly 2.200 mm x 1.080 mm (7’3″ x 3’7″)
– Feed opening 1.200 x 800 mm (47” x 31,5”)
– C.S.S. min. – max. 75 – 250 mm (3″ – 10”)
– Capacity up to 600 tonnes / hour
– Full hybrid electric driven, energy saving version
– Removable feed hopper and feeder with scalper for transport
– Intake hopper suitable for wheel loader and excavator, 6 m³
– Hydraulic gap adjustment to safely prevent clogging
– Smart sequential auto start/stop from remote
– Ability to track while producing
– 2 speed track drive
– Extensive option list to configure to your application
– Removable engine /generator compartment
IMPACT R SERIES
IMPACT R SERIES
Applications
- Limestone and many other low and medium abbrasive natural rock
- Concrete and landfill recycling
- Primary and secondary crushing
- Yard clean up
- Demolition
Quarrying and mining
- Gravel
- Asphalt
- Coal and others

– Equipped in closed circuit < 30.000 kg, easy to transport without permit
– Hopper 3,5 m³
– Vibrating feeder with punched plate pre screen 1.200 mm x 920 mm (4’ x 3’)
– Due to integrated pre screen, higher crushing capacities and less wear
– Inlet opening (H x W) 770 x 960 mm (30” x 38’’)
– Superior rotor diameter 1.100 mm (44”)
– Optional 3rd impact panel as milling beam to produce high value end product
– Optional single deck after screen, 2.800 x 1.200 mm. On R3e 3.100 x 1.400 mm (9’ x 4’)
– Capacity up to 250 tonnes / hour
– Load sensing hydraulic system reduces fuel usage by 25%
– 2 speed track drive
– Highest reduction ratio
– Superior product shape
– Extensive option list to configure to your application
– Optional windsifter
– Hopper 5 m³
– Independent 2-deck pre-screen 2.200 x 1.000 mm (7’ x 3’)
– Due to long pre screen, higher crushing capacities and less wear
– Inlet opening (H x W) 800 x 1.050 mm (31” x 41”)
– Rotor diameter 1.260 mm (50”), rotor width 1.000 mm (39”)
– Swiveling oversize return conveyor / stockpile conveyor
– Optional single deck after screen 3.300 x 1.500 mm (11’ x 5’), 4,95 m²
– Optional double deck after screen
– Also available in Electric version with direct driven Rotor by Diesel engine
– Patented tilting chassis
– Capacity up to 350 tonnes / hour
– Load sensing hydraulic system reduces fuel usage by 25%
– 2 speed track drive
– Highest reduction ratio
– Superior product shape
– Extensive option list to configure to your application
– Optional windsifter
– Hopper 7 m³
– Independent 2-deck pre-screen 3.100 x 1.250 mm (10’ x 4’)
– Due to long pre screen, higher crushing capacities and less wear
– Inlet opening (H x W) 970 x 1.300 mm (38” x 51”)
– Very robust HB 450 rotor; diameter 1.276 mm (50”), rotor width 1.250 mm (49”)
– Optional 2 deck after screen 4.500 x 1.500 mm (15’ x 5’), removable with standing legs
– Swiveling oversize return conveyor / stockpile conveyor
– Also available in Electric version with electric or direct driven Rotor by Diesel engine
– Patented tilting chassis
– Capacity up to 500 tonnes / hour
– Load sensing hydraulic system reduces fuel usage by 25%
– 2 speed track drive
– Dolly transport system available
– Highest reduction ratio
– Superior product shape
– Extensive option list to configure to your application
– Optional windsifter
CONE H-SERIES
CONE H-SERIES
Applications:
- Abrasive and hard stone
- Hard rock and ore
- Granite and basalt
- Primairy, secondary, tertiary or quarternary crushing
- River and sea gravel
- Quarrying and mining
- Production of aggregates for asphalt, concrete and others
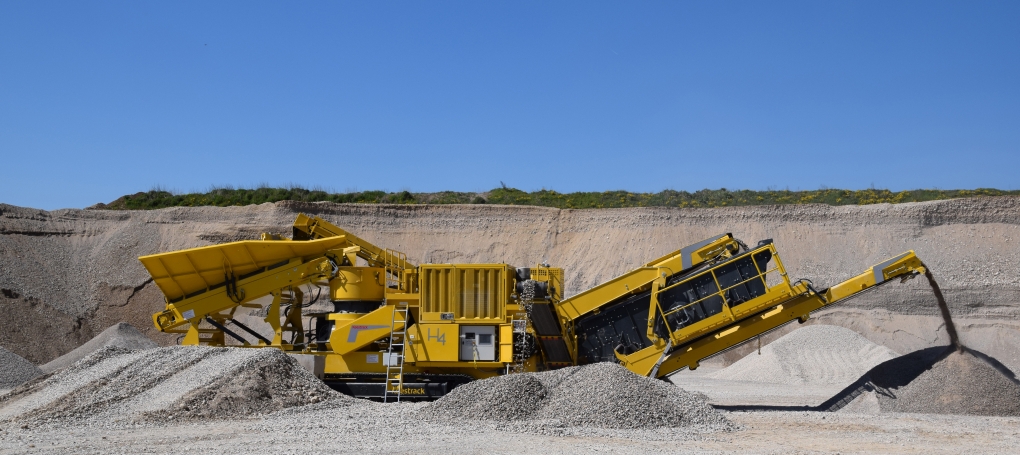
– Designed to crush the toughest of rock and ore
– Feed size up to 185 mm (7”)
– C.S.S min. – max. 6 – 38 mm (2/10”-1 5/10”), depending on crushing chamber configuration
– Capacity up to 250 tonnes / hour
– Hopper 8 m³
– Other configurations possible with different crushing chambers
– Diesel / electric drive
– 2 speed track drive
– Optional pre screen 1.200 mm (4’) x 1.800 mm (6’) *not available in the United States
– Optional 3-deck screen 3.600 mm (12’) x 1.500 mm (5’)
– Effective screen area 5,4 m² on each deck, with return conveyor
– Best product shape
– Extensive option list to configure to your application
– Removable engine /generator compartment
– Designed to crush the toughest of rock and ore
– Feed size up to 215 mm (8 5/10”)
– C.S.S min. – max. 6 – 44 mm (2/10”- 2”), depending on crushing chamber configuration
– Capacity up to 400 tonnes / hour
– Hopper 8 m³
– Other configurations possible with different crushing chambers
– Diesel / electric drive
– 2 speed track drive
– Optional 3-deck screen: Top: 4.640 mm x 1.800 mm, Middle and bottom 4.500 mm x 1.800 mm (14’9″ x 5’10”)
– Effective screen area 8,1 m² on each deck, with return conveyor
– Best product shape
– Extensive option list to configure to your application
– Removable engine /generator compartment